Vous êtes-vous déjà réveillé un matin avec une idée un peu folle en tête, tel un projet qui vous permettrait de vous stimuler intellectuellement, d’occuper vos temps libres et vous aiderait à vous accrocher à quelque chose en attendant sagement le retour de la neige? Pour certains d’entre nous, cette idée folle est d’acheter le Mont Alta (qui, soit dit en passant, est une excellente idée); dans mon cas ce fut de fabriquer une paire de skis alpins artisanaux…
J’ai toujours eu plusieurs paires de skis dans mon garage, mais j’avais toujours rêvé de posséder une « vraie » paire de skis pour la poudreuse. Par contre, l’idée de dépenser 1000$ pour une paire de skis qui me servirait à peine quelques jours par année freinait mon enthousiasme. Ainsi, un matin, un éclair de génie traversa mon esprit : pourquoi ne pas joindre l’utile à l’agréable et m’en fabriquer une? Pour la plupart d’entre vous, cette possibilité ne vous a probablement jamais effleuré l’esprit, vous disant sans doute que ça doit être extrêmement compliqué, même impossible à réaliser à la maison. Ce n’est peut-être pas simple, mais je vous assure que c’est loin d’être aussi sorcier que ça en a l’air! Lors de mon passage à l’université, j’ai étudié les matériaux composites, alors je trouvais que de m’atteler à la tâche de fabriquer une paire de ski allait être une belle occasion de mettre en pratique ce que j’avais appris à l’école.
La première étape dans la fabrication d’un ski est de déterminer les dimensions et le profil recherché. Plusieurs idées saugrenues m’ont traversé la tête, mais j’ai finalement décidé de rester conservateur dans mon approche et de confectionner quelque chose de similaire à ce qu’on trouve sur le marché. J’ai donc ouvert mon DAO (logiciel de dessin assisté par ordinateur) et j’ai commencé à dessiner mon ski. Mon choix s’est arrêté sur les mensurations suivantes :
Longueur : 196 cm
Largeur : 95-125-105-115-95
Cambrure : Rocker, camber, rocker
Une fois le concept établi, on doit passer aux choses sérieuses. Pour commencer, il faut savoir qu’un ski n’est (généralement) rien d’autre qu’un assemblage de bois, fibre de verre, de polyéthylène, de carres en acier, collés les uns aux autres, grâce à de la colle époxy. On assemble les composantes les unes par dessus les autres dans un moule et on applique une pression (ou on effectue un vide dans mon cas) pour permettre à chacune des couches de bien adhérer entres elles.
Le noyau de bois
Le tremble, le frêne, l’érable, le peuplier et même le bambou (pour ne nommer que celles-là) sont des essences de bois fréquemment utilisées dans l’industrie du ski. Idéalement, pour faire notre choix, on doit prendre en considération le type de ski qu’on désire fabriquer; un ski haute performance dédié à la course aura besoin d’être robuste et plus rigide qu’un ski de touring ultra léger.
Le peuplier, par exemple, est un bois très léger, environ 0,4 gramme par centimètre cube. Un noyau uniquement conçu en peuplier permettrait d’avoir un ski extrêmement léger, par contre, sa flexibilité et ses propriétés mécaniques (résistance) laisseraient à désirer. Ce type de bois pourrait donc convenir à la fabrication d’un ski de « touring » où on essaie de minimiser au maximum le poids du ski. L’érable, quant à lui, est beaucoup plus résistant, mais son poids se chiffre plus aux alentours de 0,6 gramme par centimètre cube. Plus rigide et plus résistante, cette essence serait plus judicieuse pour un ski de carving.
Dans mon cas, mon noyau est constitué de frêne; pour la simple et bonne raison que j’avais des morceaux de frêne qui traînaient dans le garage. Afin de s’assurer que le noyau soit exempt de faiblesses et d’irrégularités dans le grain, il est recommandé de laminer ensemble plusieurs languettes de bois d’environ ¾ pouce (19-20mm) avec de la bonne veille colle à bois.
Une fois la colle séchée, on peut aplanir notre noyau grâce à un planeur et lui donner le profil désiré. Bien que les spatules puissent être confectionnées en bois, il est recommandé de les fabriquer en plastique (généralement de l’abs). Le plastique est plus résistant à l’impact que le bois, donc avec l’emploi de celui-ci, il en résulte un ski plus durable.
La semelle du ski
Dans mon cas, puisque j’avais dessiné mon ski dans le DAO, j’étais en mesure de faire imprimer le design du ski grandeur nature sur une feuille de papier. Il était donc simple de tracer et ensuite découper dans une feuille de polyéthylène mes semelles de ski. Une fois découpées, j’ai collé mes semelles sur du ruban adhésif deux faces dans mon moule et j’ai collé « temporairement » mes carres d’acier avec de la « crazyglue ».
La vraie liaison entre la semelle et les carres a lieu lors du laminage. Cette étape consiste à étendre une couche de fibre de verre sur la base du ski et à la recouvrir de résine époxy. On peut ensuite déposer le noyau de bois sur la couche de fibre de verre puis appliquer une dernière couche de fibre de verre. Après, on applique la couche finale constituée habituellement d’un graphique imprimé sur un film de plastique; dans mon cas, j’ai choisi une couche de fibre de carbone.
Une fois le laminage complété, on doit s’assurer d’avoir une bonne cohésion entre les couches en appliquant une certaine pression sur celles-ci. Il existe deux méthodes courantes dans la fabrication de skis, soient la presse à ski et le moulage sous vide. Le moulage sous vide demande un moule moins robuste et est beaucoup plus facile à mettre en œuvre pour une fabrication unique, c’est donc la technique que j’ai privilégiée. Le principe est simple: on applique une pellicule de plastique par-dessus notre laminage et on scelle tout le contour de notre moule à l’aide d’une gomme. On fait le vide à l’intérieur du plastique grâce à une pompe à vide, une pression est donc appliquée uniformément sur notre assemblage. On laisse sécher la résine durant une nuit et le ski est presque terminé.
Une fois bien séché, on peut retirer le ski du moule. Il ne reste plus qu’à découper l’excès de bois et de fibre de verre sur le contour du ski, puis, procéder à un petit sablage, installer une paire de fixations et attendre (im)patiemment la prochaine bordée de neige! J’ai d’ailleurs testé mes propres skis en piste… un super sentiment de plaisir et d’accomplissement!
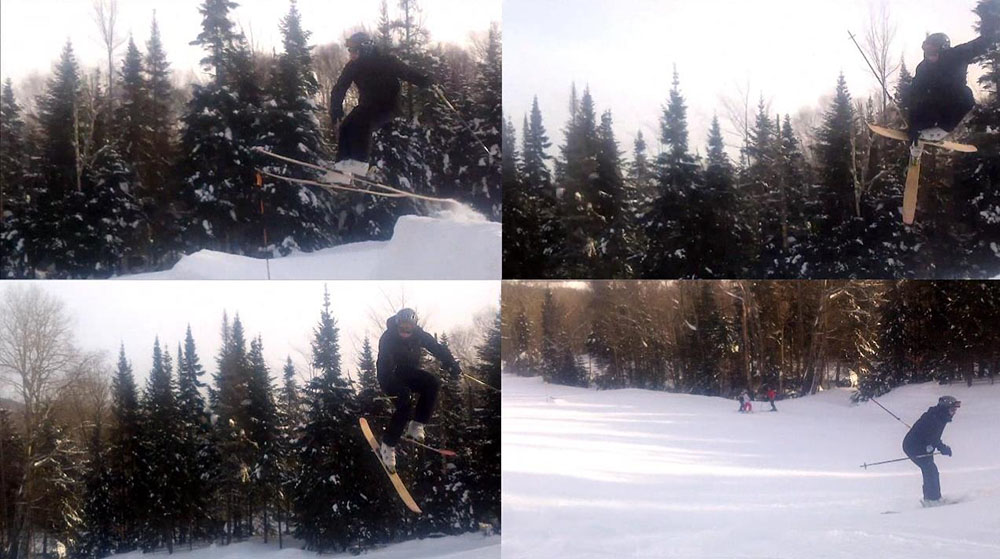
Pour ceux qui seraient intéressés à se lancer dans la fabrication de skis artisanaux, retenez qu’il en coûte moins de 200$ pour le matériel nécessaire à la confection, et que j’y ai mis environ 50 heures. Voici quelques sites internet qui peuvent vous aider:
– www.skibuilders.com (en anglais) qui explique en détails les diverses étapes de fabrication et indique où se procurer les divers matériaux (qui sont difficilement trouvables au Québec, malheureusement)
– Freeman Supply, pour la fibre de verre et la résine
– Blank Slate Skis, pour d’autres matériaux